- High School
- You don't have any recent items yet.
- You don't have any courses yet.
- You don't have any books yet.
- You don't have any Studylists yet.
- Information

Goodman-Company-Case Sample
Fundamentals in accounting (acc101), laguna northwestern college, students also viewed.
- Confidence Interval 1 17
- Flowchart on Hypothesis Testing
- Accounting-for-business-combination-with-answers compress
- Article-1207 - reviwerrrrrrrrrr
- Unenforceable contract
- Lawrfbtreviwerrrrrrrrrr
Related documents
- reviwerrrrrrrrrr
- ARCH203 Handout 10
- Actividad T8 - Apuntes
- Excel Shortcut List
- A variable is any factor or property that a researcher measures
- Corporation Notes in intermediate accounting
Preview text
Department of Agribusiness Management and Entrepreneurship College of Economics and Management University of the Philippines Los Baños College, Laguna MGT 231: HUMAN BEHAVIOUR IN ORGANIZATION 1 ST SEMESTER AY 2018- 2019 CASE NO. 4 GOODMAN COMPANY GROUP NO. 2 SECTION-UW AVENIDO, ARIANE _________________ BAUTISTA, KARMELA _________________ CRISTE, CRISSELLE _________________ GARCIA, ANTON _________________ MANGLO, JOANNE MARIE. _________________ MALINAO, GLACELLE ALYNE _________________ DATE SUBMITTED: 01 December 2018
I. POINT OF VIEW
The point of view of the President of the company Robert Goodman will be taken. As the owner of the company, he is the one who has direct influence on what are the possible actions the company can do. In addition, he is the one who decided to hire a production analyst to improve the efficiency of its operation. II. PROBLEM STATEMENT What action should Mr. Robert Goodman and the management of the company do to manage the decreasing output of Shift 1 and Shift 2 and to turn around the total company performance and make it more productive? III. CASE FACTS (DO A SWOT ANALYSIS INSTEAD) ● Mr. Goodman is the President of the Goodman Company. ● The company considered making a multi-million dollars’ worth of expansion but due to limited funds, Mr Goodman decided to depend on the productivity of the current machines of the plant. ● Mr. Goodman decided to hire a Production analyst which will be responsible assessing the process of the plant and generate recommendations to increase its productivity. ● The production process before was a job shop production process where each worker is paid on a per hour basis. ● The production process after the recommendation of Ms Ann Bennet will be on a Mass production format. ● Prior implementation of the changes in process, first shift never loses in production and the level of quality is top- rate ● due to the workers participation in planning the weeks production as well as having someone (Fireball) take note of all the problems and improvement suggestion. ● The first shift supervisor, Cleverson Anthony, is highly respected by top management since he has been with the company since 1965 and is set to retire in eight years. He has no real need to work since he was left an inheritance by his brother-in-law which caused him to have 6-week long vacations without thinking about what happens in the production of his team. ● Two other persons in the first shift have been mentioned to be informal leaders in the group. These being Joe and John. Joe because he felt he has seniority over the others because he was hired on the same day as Clev, and John because he
● Gender bias was expressed by Norm because he thinks that if Ms. Bennet’s program was thought off by a man, workers would have been more willing to adopt the new process. ● Third shift is composed of 5 full time employees and 7 college students which was hired for the summer. The members of this shift have bonded and communicate with each other freely during their shift making cooperation within the group extremely high. The supervisor, Bob Jackson, works together with the production staff whenever they are having difficulties. The third shift also makes it a point to gather after work to bond over beer. ● Bob Jackson was a 29 - year-old ex-marine sergeant who thought that he did not need to constantly push his team hard to make the production quotas. He along with his group are relatively new compared to the other shifts his they have no one who worked for the company for more than five years. He underwent three weeks of extensive training in all aspects of the operation before being assigned as supervisor. The members of his shift had also spent two weeks familiarizing themselves with the operations, a learning curve that enabled them to get used to procedures ● When top management decided to implement Ms. Bennet’s new procedure, only Bob talked to his team and told them of the roles that would be needed in the new system which prepared the group for the changes about to be implemented. ● Despite implementing the new process proposed by Ms. Bennet, the workers of third shift are motivated and actively suggests other ideas that will make the process easier, and their shift will be more productive ● The third shift had a system of rotating operators. The team often does races of who could produce more products between two groups to break the boredom of work. And to avoid lowering the quality of the production, Jackson designed an elaborate scoring system that penalizes any group for defects. This often leads to the team reaching the quota within five hours. As a reward, Bob allows his members to have longer lunch breaks. He also does not set a new quota for the third shift despite them being capable of producing more than the required amount of goods. By doing this, he avoided giving his team additional stress of meeting a higher quota. ● Workers of the first and second shifts have been in the company for more than seven years which means that they have stronger muscle of the old process compared to the third shift who have five regular employees with less than five years’ experience as well as seven college students who have a better tendency in adapting to changes in processes.

IV. ALTERNATIVE SOLUTIONS
Alternative 1: Conduct team building activities for the first and second shifts as well as give them additional trainings to improve their performance for each task/role in the new system. Pros: ● Will increase the workers’ teamwork. ● Will allow the two shifts to get used to the new procedure and their corresponding roles Cons: ● Older employees might think it is a waste of time ● Will require additional cost Alternative 2: Meet all the employees of the company and discuss the advantage of implementing the proposal of Ann Bennet. Pros: ● Easy to implement ● No additional cost ● Will make the workers understand the need for increased productivity ● Will motivate the employees to work harder Cons: ● Might cause argument within the workers ● Some might not be attentive during the meeting/speech of Mr. Goodman Alternative 3: Robert Goodman should have a meeting with Anne Bennet to discuss & analyze the result of her new manufacturing process program to come up with an immediate corrective & preventive action plan, which will be implemented immediately to have an effective program, efficient workers, and productive company. The goal of this alternative is to focus on improving organization’s current production process, to eliminate existing undesirable situations in different shifts and to identify unnecessary causes of errors & non-conformities among workers. This will promptly address the challenges that the company is currently facing. Pros: ● Solution will have scientific basis ● No additional cost to be incurred ● Top management will be personally involved coming up with a solution
Productivity effectiveness will measure how much increase in output will be made using a particular alternative. Usability will be measured based on how usable the solution be in the problem. Promptness will be measured in terms of how long the results of the alternative can be seen. V. DECISION After thorough consideration of weights given on each decision criteria, the group chose Alternative 2, meet all employees of the company, and discuss the advantage of implementing the proposal of Ann Bennet as the best option for Mr. Goodman to address the problem of the company. In this alternative, Top management will conduct a meeting with the employees to explain to them the reason a new system is put into place VI. IMPLEMENTATION Major Activities (list based on sequence of implementation) Person/People/U nit Responsible Time Frame (duration of activities, i. 3 weeks) Where Relevant/ Critical factor(s) to consider in the conduct of activities Top management, Mr. Goodman and Anne Bennet to discuss and prepare for a presentation on highlighting the benefit in change of process. Top management, Mr. Goodman and Anne Bennet 1 day Company’ s Office - Objective of the change in process. - Current situation of the company. - Reason for hiring Ms. Bennet. - Expected output of the meeting. Discuss first to supervisor meeting agenda Top management and Supervisors 1 day Company’ s office - Solicit information/feedba ck on what is
happening in the operation.
- Explain the change in process and reason behind it.
- Solicit recommendation on how to improve the process per shift Call for a townhall. All members of the organization 2 days Company’ s multipurpo se area.
- Discuss the Objective of the change in process.
- discuss Current situation of the company.
- discuss Reason for hiring Ms. Bennet.
- Solicit feedback and recommendations on how to improve the process. Monitor and Create a feedback control mechanism top management VII. CONTINGENCY PLAN If the chosen alternative fail, the company should conduct team building activities for the first and second shifts as well as give them additional trainings to improve their performance for each task/role in the system. One of the causes of the decline in performance in Shift 1 and Shift 2 was due to the lack of teamwork unlike the shift 3. Creating a bond between the team will help each group build a trust with each other that may result to high performance. VIII. REFERENCES
- Multiple Choice
Course : Fundamentals in Accounting (ACC101)
University : laguna northwestern college.

- Discover more from: Fundamentals in Accounting ACC101 Laguna Northwestern College 55 Documents Go to course
- More from: Fundamentals in Accounting ACC101 Laguna Northwestern College 55 Documents Go to course
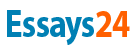
- American History (4,233)
- Biographies (1,169)
- Book Reports (3,862)
- Business (17,294)
- English (13,871)
- History Other (3,821)
- Miscellaneous (12,648)
- Music and Movies (1,106)
- Philosophy (1,165)
- Psychology (1,486)
- Religion (953)
- Science (2,671)
- Social Issues (7,924)
- Technology (1,924)
- Browse Essays
- / The Goodman Company Case Analysis
The Goodman Company Case Analysis
Essay by Matthew Herbert • October 7, 2017 • Research Paper • 2,809 Words (12 Pages) • 4,339 Views
Essay Preview: The Goodman Company Case Analysis
The Goodman Company operates one plant that manufactures small rubber automotive parts, these products are sold to assembly plants for new trucks and cars. Robert Goodman is the president of the company, under him is Joe smith who is the production manager, he reports directly to Mr. Goodman. Under Mr. Smith are three supervisors, these supervisors are: Cleverson Anthony, Norm Leonard and Bob Jackson, they each manage a one of the three shifts.
The production process was handled by each individual worker, the production process consisted of: Sheets of rubber are purchased, each worker would obtain this material and cut it down to the size of the product, they then place the material on a steam-fed curing press which consist of 12 molds, the press is then activated, while this is happening the workers trim the excess rubber from the parts, the parts are then put into boxes and moved to the shipping area.
There was an increase in demand for their product, as a result Mr. Goodman sought to increase productivity without having to purchase equipment or expand the company considering there was not money available to do these things. He then hired Ann Bennet whom is very qualified with a degree in finance, to generate recommendations for wringing greater productivity from the plant. Ms. Bennet developed a plan based on Mr. Goodman’s desires, this plan however had adverse effects which caused the output for the first and second shift to fall.
Ms. Bennetts plan meant that each worker will no longer performs the entire process and that each stage was assigned to a worker. Her plan consisted of: One worker was assigned raw material preparation, another assigned material handling, another was assigned to activate the press and put the product on a conveyer belt so that the one assigned to trim the excess rubber would receive the product.
The first shift department was considered to runs itself,what the first shift supervisor is Cleverson Anthony who was to retire in 8 years’ time. The shift production output was good and the quality of the products were considered to be very high according to Cleverson Anthony and Fireball. However the shift workers felt like the company did not appreciate them considering they felt like they contributed allot to the company over the years..
After the plan was implemented Cleverson asked for early retirement. The shift began to complain of the new process, and the products quality fell as well as the output. They were also upset that they were now being paid a per piece rate instead of an hourly rate. This also pushed the belief further that they were unappreciated because there work was simplified.
The second shift supervisor is Norm Leonard, he had only worked at the company for three years as a means of extra money to ease the transition into retirement. The shift workers have worked at company for 7 to 8 years and they did not accept him with open arms. Norm’s job is considered easy because when the workers have problems they go to Jim Flask who is a senior man on the shift, who knows how every product and machine should be. Jim is trusted and liked by his fellow workers.
After there was a dramatic decrease in production as a result of the change. Jim Flask was reassigned as the shift set-up man and mechanic because of his experience. Norm believe that the largest decrease in production was due to this, considering Jim had a higher production rate than the others and he also believed that the plan was being rebelled against because it was implemented by a woman.
The supervisor for shift three was Bob Jackson his management style is hands on and relationship oriented. He did not believe that he constantly had push workers to reach the company's production quota. He worked side-by-side with his members who are experiencing difficulty with their machinery or materials. This shift was made up of 12 workers they all socialise among members even after work. They were very cooperative with each other and helped fellow employees with mechanical or material difficulties. Bob Jackson notified his shift of the change in production process.
After the change Bob Jackson suggest a job rotation between employees as operators so that they would not grow bored of the repetition which would later lead to low production output and lack of motivation. He also encouraged the workers to break up into two teams and challenge each other in a production race to encourage productivity and motivate them. To ensure that quality of product did not suffer he implemented a scoring system that penalized any gr for defects. He also encouraged their ideas in making their work easier. This caused the shift to out produce both shift one and two.
Core Problem
Ineffective Management was identified as the core problem. Management is defined as the organization and coordination of the activities of the business in order to achieve defined objects. Leadership is defined as the ability to influence a group towards the achievement of a vision or set of goals. Henry Mintzberg classified Managerial Roles into three groups, these groups are: Interpersonal, Informational and Decisional (Robbins and Judge, 2013, P. 6-7).
Interpersonal roles deals with interacting with the workers for the purpose of achieving organizational goals. Interpersonal consist of: Figurehead, Leadership and Liaison. Informational deals with the collection of data/ information in order to achieve the companies goals i.e. Media and internet. Informational consist of: Monitor, Disseminator and Spokesperson. Finally, the Decisional role deals with making decisions based on the informational role. Decisional consist of: Entrepreneur, disturbance handler, resource allocator and negotiator.
Bob Jackson adheres to the roles of an effective manager and understands his role. While Cleverson and Norm failed to adhere to all the roles of an effective manager and did not understand their roles. A figurehead is the social and legal duties that a manager is required to perform. A leader is in charge of motivating, training and discipline workers. As a liaison a manager is required to obtaining feedback and information from external contacts. In regards to the Supervisors Cleverson and Norm they both were unable to motivate their workers, and in the case of Norm not disciplining his workers after they would goof off which was part reason for the fall in production output. In the case of Cleverson his workers felt undervalued
Monitor is the job of obtaining information about the internal and external changes in the companies’ environment and monitoring the performance of employees and their productivity. Disseminator is the act of relaying information from employees or external sources to the company head. Spokesperson is the job of supplying outside sources with information on the company. It would appear that all supervisors did adhere to this roles, as far as Cleverson is concerned he and Fireball would go to the office to inspect a product that was returned and conclude it was one of the other shifts. Norm was aware that Jim flask had a higher output rate than his fellow workers in shift 2. Bob implemented a competition and scoring system to increase output from each individual as well as ensure high quality.

COMMENTS
Goodman uses best practice sustainable techniques and materials to enhance the long-term sustainability of our properties, and reduce our impact on the planet. ... Global meal kit company HelloFresh is on a mission to change how people eat, forever. About Goodman. $6.6bn ... Sustainability case studies. Sustainability case studies.
Goodman Foundation case studies . See how we make a tangible difference. Sustainability case studies . Learn more. Our customers Our customers and industries. Logistics. ... Sustainability case studies. Sustainability case studies. Goodman is committed to high quality. We use best practice sustainable techniques and materials to enhance the ...
Resources and case studies. At Goodman, we use best practice sustainable techniques and materials to enhance the long-term sustainability of our properties, and reduce our impact on the planet. ... Global meal kit company HelloFresh is on a mission to change how people eat, forever. About Goodman. About us.
Goodman's properties are designed to continue to be efficient and highly functional long into the future. ... Case studies. At Goodman, we think of sustainability as a team sport in which everyone has a role to play. If we want to transition to a low-carbon future, we all need to help one another by collaborating and sharing across businesses ...
The Goodman Case Analysis February 25th,2019 Group Introduction Ladisha Boyce Gaybriella Griffifth Akayla Corbin Shaneya Moffie Abigale Bignall Faith Johnson Introduction Company Goodman Company - Manufacturer - Management layout -Productivity levels -Hire production analyst Do you
Essay on Goodman Company Problem Statement How did the sudden adoption of a newly conceived production process, aimed at increasing efficiency, affect the performance of workers ... Goals were not communicated to them in this case. Therefore lack of communication, leadership skills, not involving supervisors in decision making all led to ...
Read this Business Case Study and over 74,000 other research documents. Goodman Company Case Study. Case Study The Goodman Company I. Point of View Mr. Robert Goodman - He is the President of Goodman Company which is a single plant manufacturing company which produces small rubber automotive parts; the company has a centralized, bureaucratic organizational structure.
Department of Agribusiness Management and Entrepreneurship College of Economics and Management University of the Philippines Los Baños College, Laguna MGT 231: HUMAN BEHAVIOUR IN ORGANIZATION 1 ST SEMESTER AY 2018- 2019 CASE NO. 4 GOODMAN COMPANY GROUP NO. 2 SECTION-UW AVENIDO, ARIANE _____ BAUTISTA, KARMELA _____ CRISTE, CRISSELLE _____ GARCIA, ANTON _____ MANGLO, JOANNE MARIE.
Read this Business Research Paper and over 74,000 other research documents. The Goodman Company Case Analysis. _____ Background The Goodman Company operates one plant that manufactures small rubber automotive parts, these products are sold to assembly plants for new trucks and cars. Robert Goodman is the president of the company, under him is Joe smith who is the production manager, he reports ...
Sustainability case studies Sustainability case studies. Sustainability case studies. No two Goodman properties are the same. From acquiring pre-loved land, to recovering and recycling materials for re-use, to transforming historic sites into modern facilities equipped to face the future — every single one of our sites has a story to tell ...